
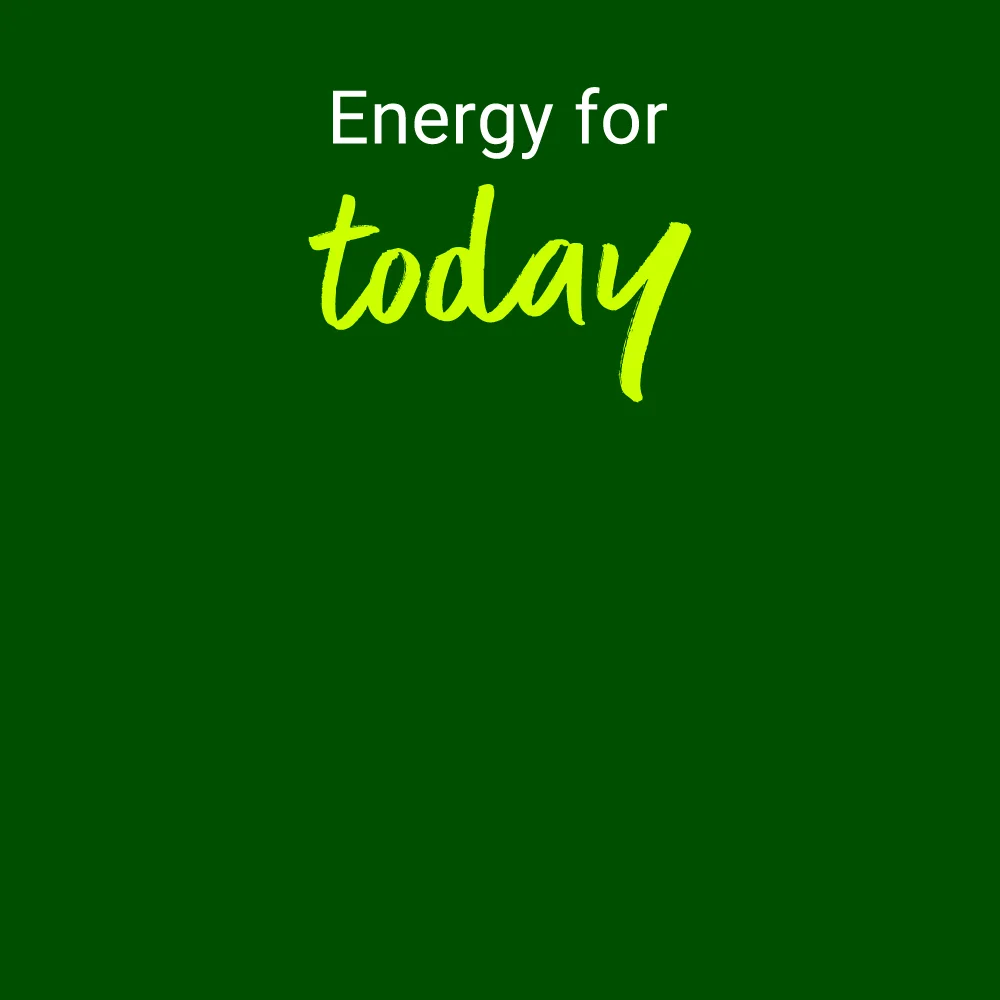

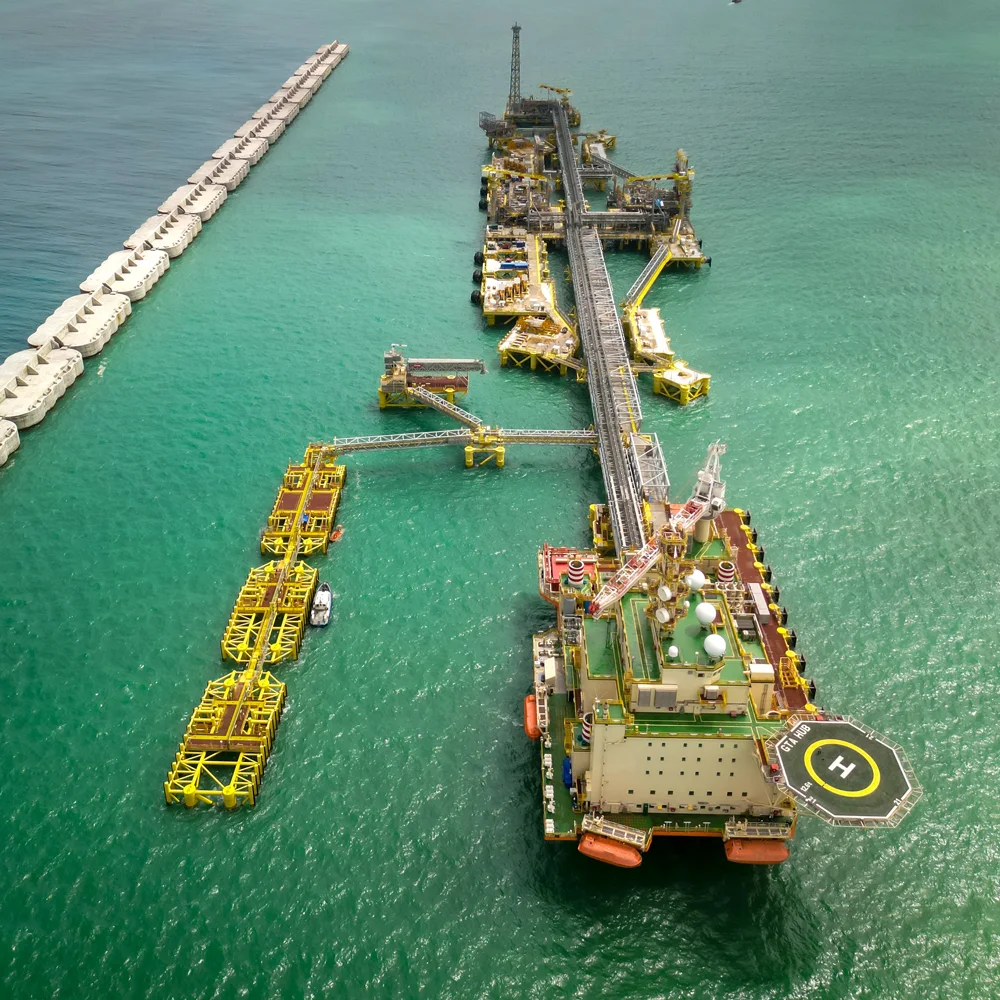
Engineering is at the heart of our work to keep production flowing.”
Medhat Hegazi

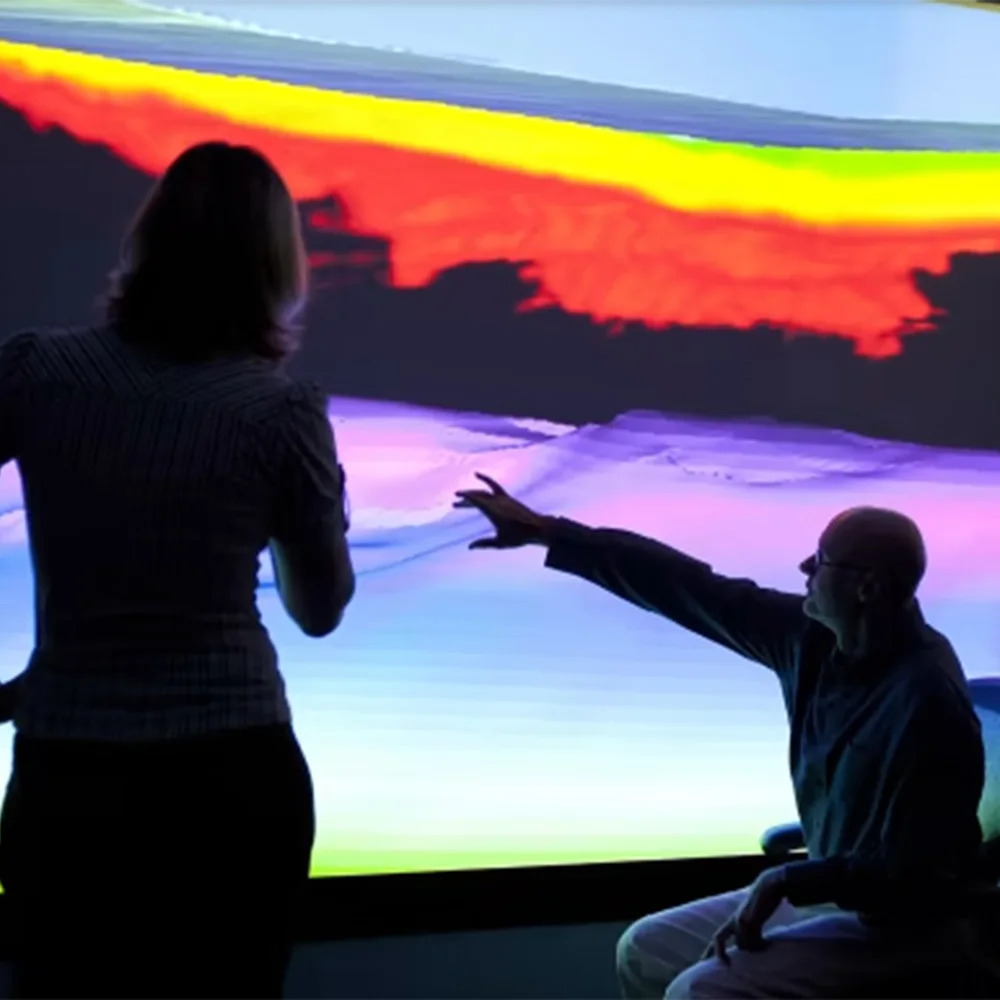
Keeping gas flowing
MEDHAT HEGAZI

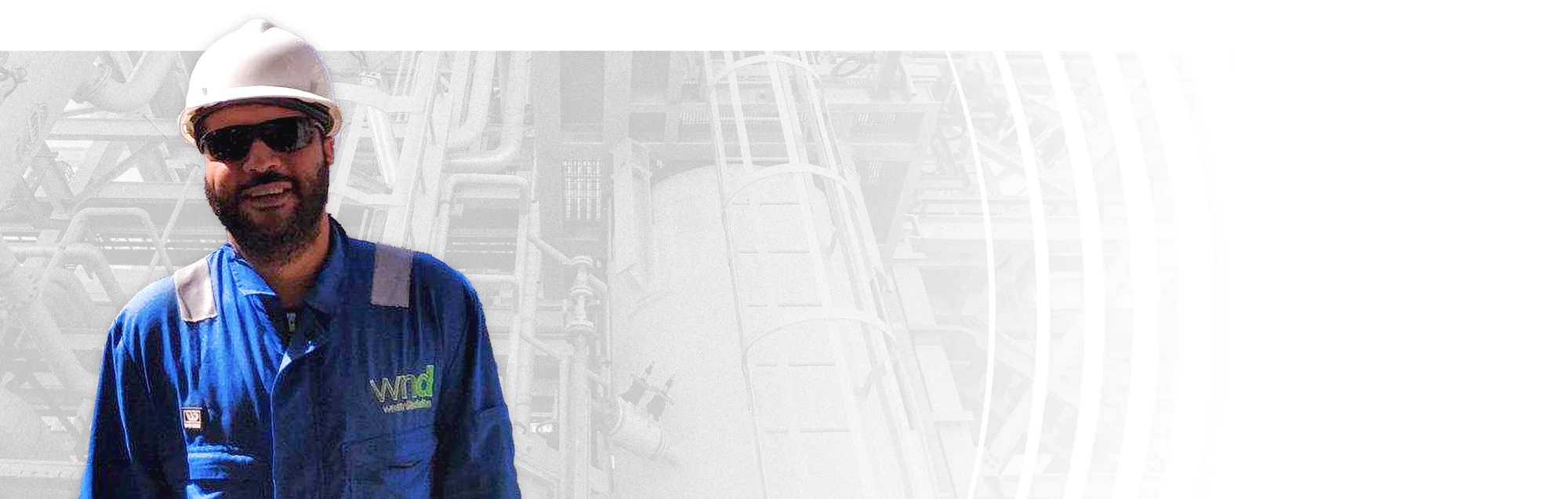
Keeping gas developments running safely and reliably requires constant monitoring and maintenance.
That’s the challenge facing Medhat Hegazi, an integrity, inspection and fabric maintenance squad lead at bp’s West Nile Delta (WND) development, off the coast of Egypt in the Mediterranean.
Medhat and his team work to support the safe and efficient operation of the equipment used at bp’s five fields across the WND development, helping to meet production targets while working to minimize downtime and assess risks.
“We use technology as much as possible, especially for routine inspections,” explains Medhat, who is based in Cairo. “For example, drones assist us in gathering data, including methane measurements, while also helping to keep personnel away from potentially hazardous areas.”
The WND development was bp’s first operated asset in Egypt. Since it began operations in 2019, it has contributed to increasing energy supply in Egypt. This year, bp and ADNOC agreed to form a new joint venture to focus on the development of gas assets in Egypt.
“The West Nile Delta’s operations are designed to maintain high reliability and efficiency rates,” says Medhat. “Engineering plays a crucial role in our efforts to ensure production continuity.”
Back to top
Maximizing production
DINA MENDES

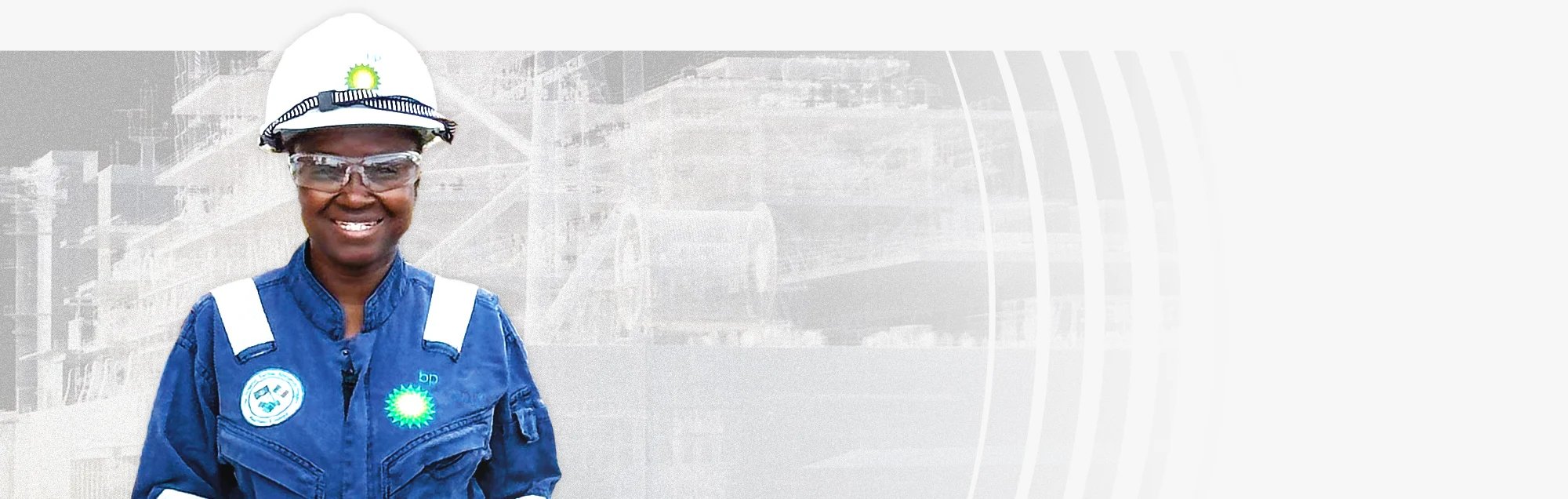
The Greater Tortue Ahmeyim Phase 1 mega gas development off the coasts of Mauritania and Senegal is one of bp’s largest and most complex projects ever.
With so many moving parts, delivering LNG to the market on time and at the required volume will be a major challenge when the development starts up.
That’s the job of engineer Dina Mendes and her team, who are responsible for managing the delivery of gas from reservoir to the LNG carriers for export. When production starts, the development is expected to produce up to 2.4 million tonnes of liquefied natural gas (LNG) a year.
“Our focus is on setting up the tools, processes and integrated ways of working to deliver year on year. My team and I have an exciting challenge ahead to maximize value to our partners and host countries, while keeping safety as our first priority,” says Dina, who was born in Angola and moved to the UK in 2017.
“This project is unique on so many fronts, from the fact that the development is solely offshore, to its cross-border location. For so many of the things we are doing here, there is no precedent to call on – that’s what makes it so exciting.”
Engineering in the ultra-deep
BRANDON JAMES

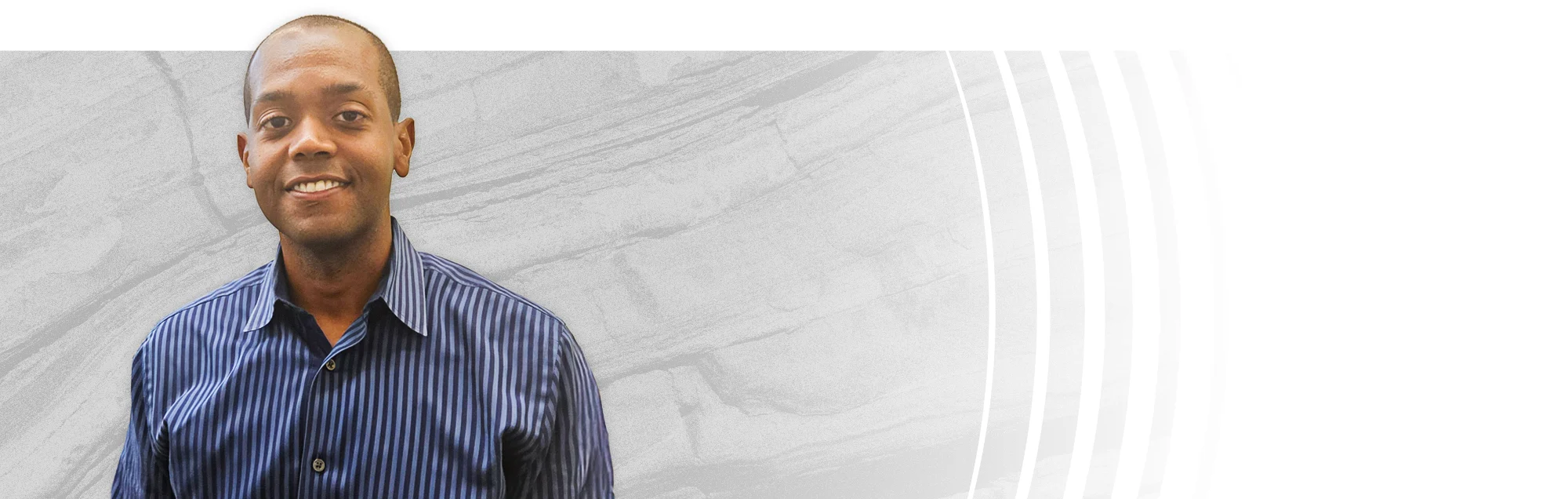
The Kaskida field in the Gulf of Mexico requires more complex engineering than any prior bp project.
Located in ultra-deep reservoirs, it can only be developed with specialized techniques and equipment capable of withstanding high pressure and high temperatures.
Completions engineer Brandon James is part of the wells team now working to solve those challenges. They’re developing the safe and reliable well designs needed in this pioneering project for bp to access the underground resources and maximize production.
In the Kaskida field, the make-up of the reservoirs is uniquely complex, and Brandon works closely with colleagues in bp’s subsurface and wells teams to better understand the sands and plan the fracturing operations that create what he calls a ‘super-highway’ to direct the oil more efficiently towards the well and lift it up to the surface.
When finished, Kaskida will mark bp’s sixth operated hub in the Gulf, with the capacity to produce up to 80,000 barrels of crude oil per day from six wells in its first phase.
“It gives you a sense of pride to work on something so cutting edge and valuable to bp. You most likely won’t see a TV show about petroleum engineering, but it’s just as exciting an industry as the professions you often see portrayed on screen,” says Brandon, who lives in Houston.
Developing digital tools for engineers
ZAID RAWI

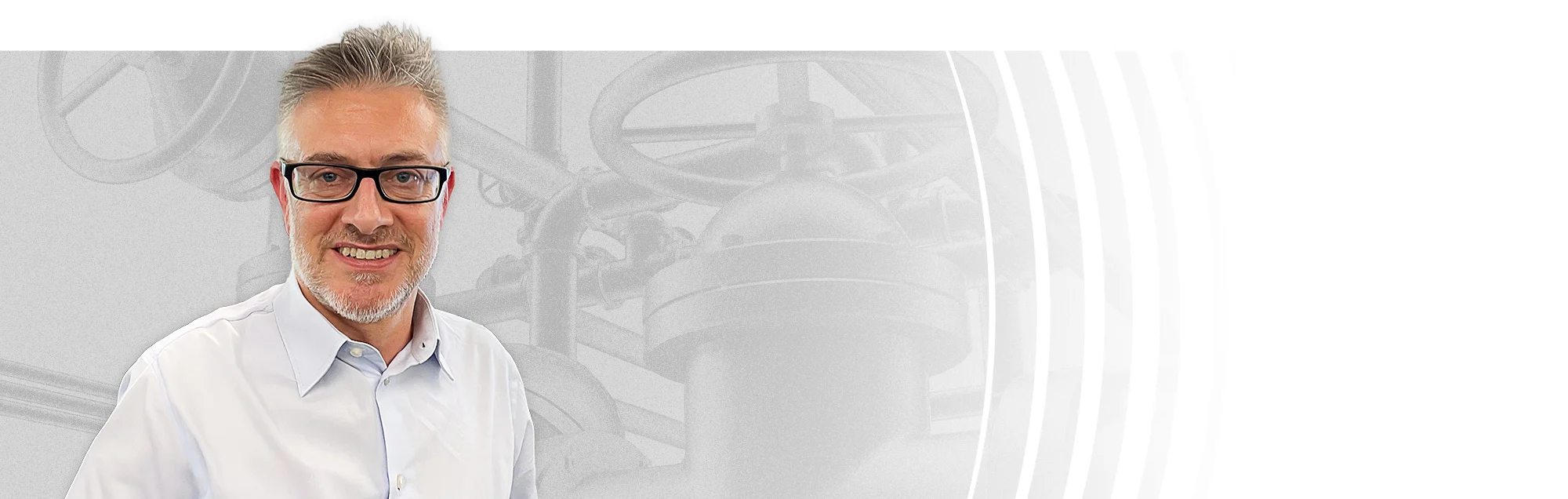
How could bp better protect its piping, vessels and other infrastructure from corrosion and erosion?
That was the challenge that digital tools engineer Zaid Rawi and bp engineering advisors needed to help solve. To do so, he and his colleagues created an app.
“The project started off with us putting our corrosion and erosion models online in real time so that our subject matter experts could better understand where there could be potential problems. Both can lead to a loss of production, or, in extreme cases, a loss of primary containment, so giving engineers these tools helps to improve safety as well as performance,” says Zaid, who joined bp 25 years ago.
Those apps were the first in a broader toolkit Zaid and his coworkers developed to help boost safety and efficiency, including the addition of models for scaling, flow blockages and vibration risk. They also help to make bp’s digital twins of oil and gas platforms more effective, so simulations and data analysis can take place without physical access. Zaid and his team help to verify that the asset engineering data supporting these models and other use cases is digitized and as up to date and accurate as possible.
“Deploying these technologies contributes to helping bp secure today’s energy supply – and the next generation of energy, too,” says Zaid, who is based in Sunbury, outside London. “It’s quite satisfying to build tools that make a difference and can be used on projects and operations around the world.”
Engineering tech tools for the future
THAIS LAUER

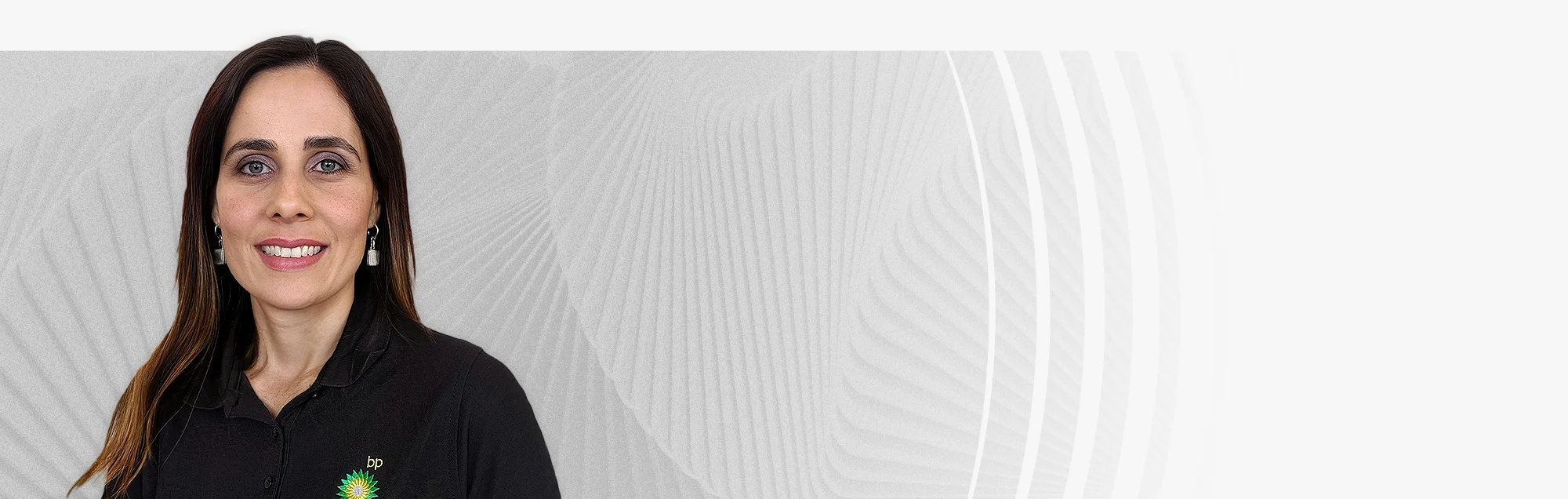
Thais Lauer doesn’t have a crystal ball, but she does try to predict the future.
As the digital science lead, her challenge is to understand and apply emerging digital technologies to bp’s businesses.
An industrial engineer by background, Thais’s focus is on emerging digital technology solutions in the fields of robotics, internet of things sensing, and trust and transparency, that could be applied to bp’s businesses.
Thais and her team start off by talking to bp’s different businesses to better understand their biggest challenges. Then, they look at academic research, talk to technology companies and think about how these emerging technologies can be applied at bp.
One of her more recent projects resulted in the development of a robotic arm to help people with accessibility needs more easily charge their electric vehicles. bp has been granted a patent for this technology and is now looking at how this could be used.
“There are many operational tasks that would be safer and more efficient if executed by a robot, so we have been searching for solutions to help with this. One of our original questions was to look at how robots have solved Rubik’s Cubes. In thinking about how something could be useful at bp, we go through a creative process and think about all possible use cases. Then, we narrow it down by looking at where there is a real customer challenge, potential to improve safety or create efficiencies,” says Thais, who is based in bp’s Sunbury office, outside London.
Her latest project focuses on how trust technologies, such as blockchain, can support renewable fuels certification to enable cost-competitive production of lower carbon fuels, such as green hydrogen.
“We need to prepare for the future to remain competitive,” Thais says. “In roles like ours, we get to experiment and test with what the future could look like.”

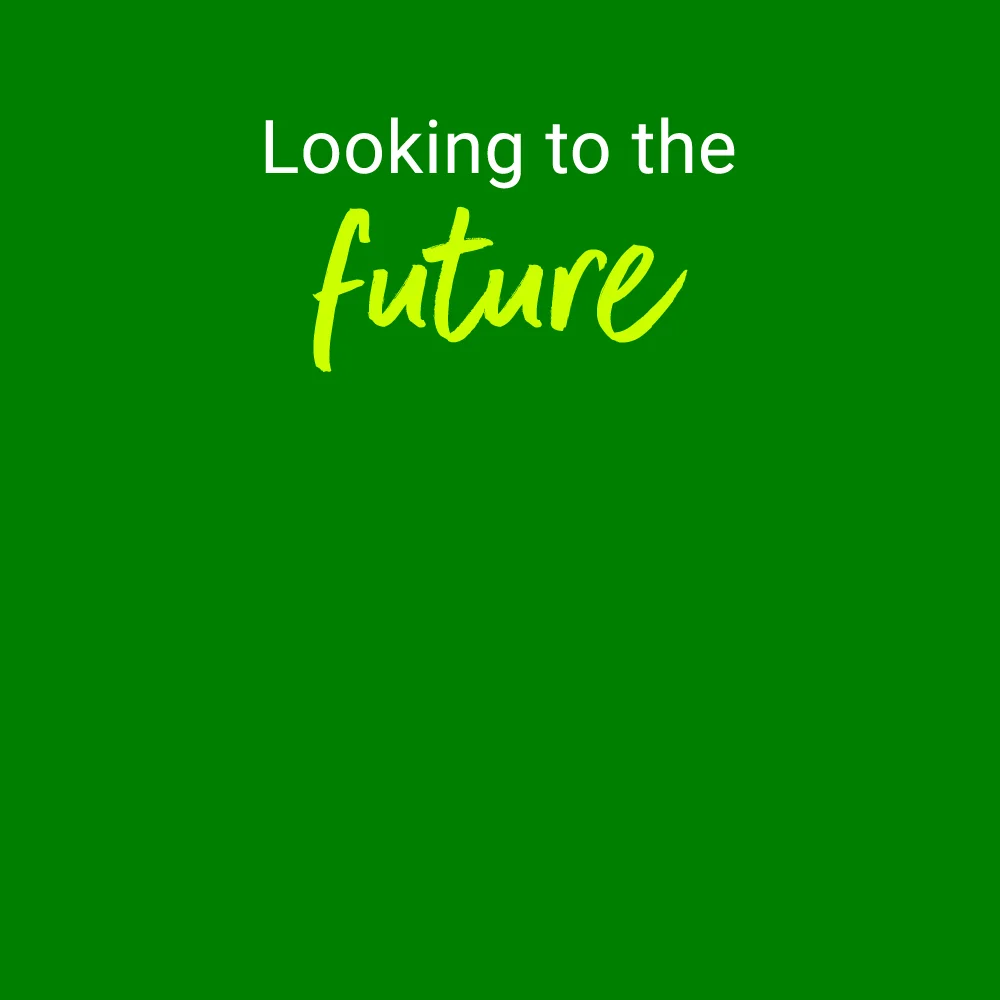

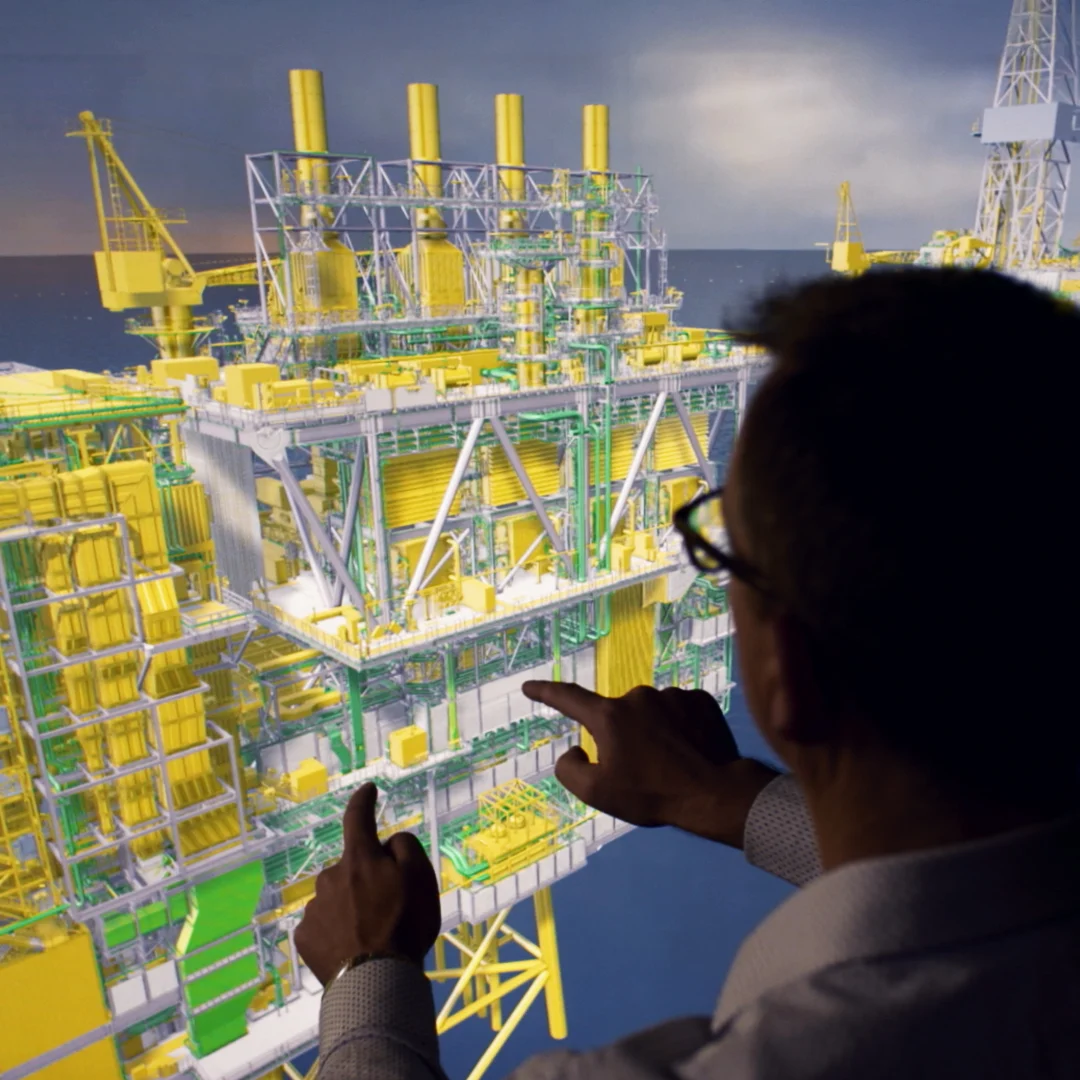
We need to prepare for the future to remain competitive.”
Thais Lauer

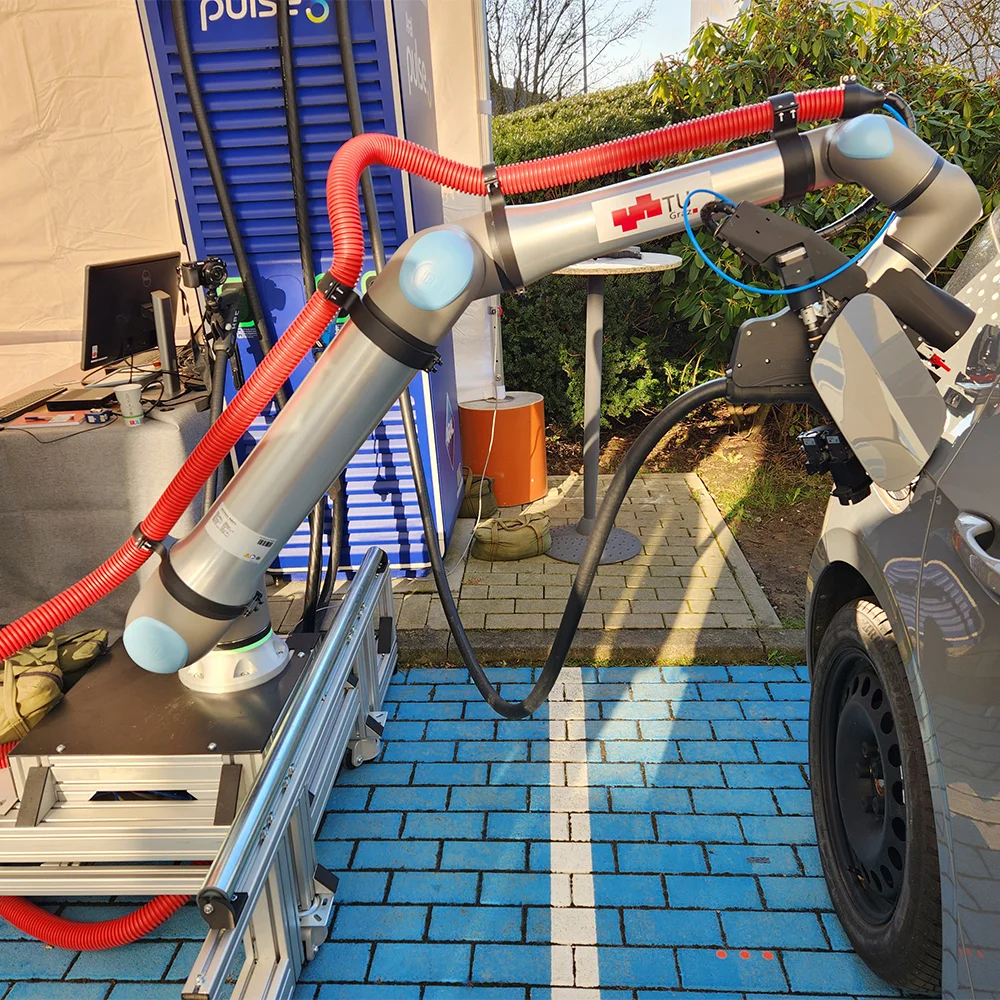

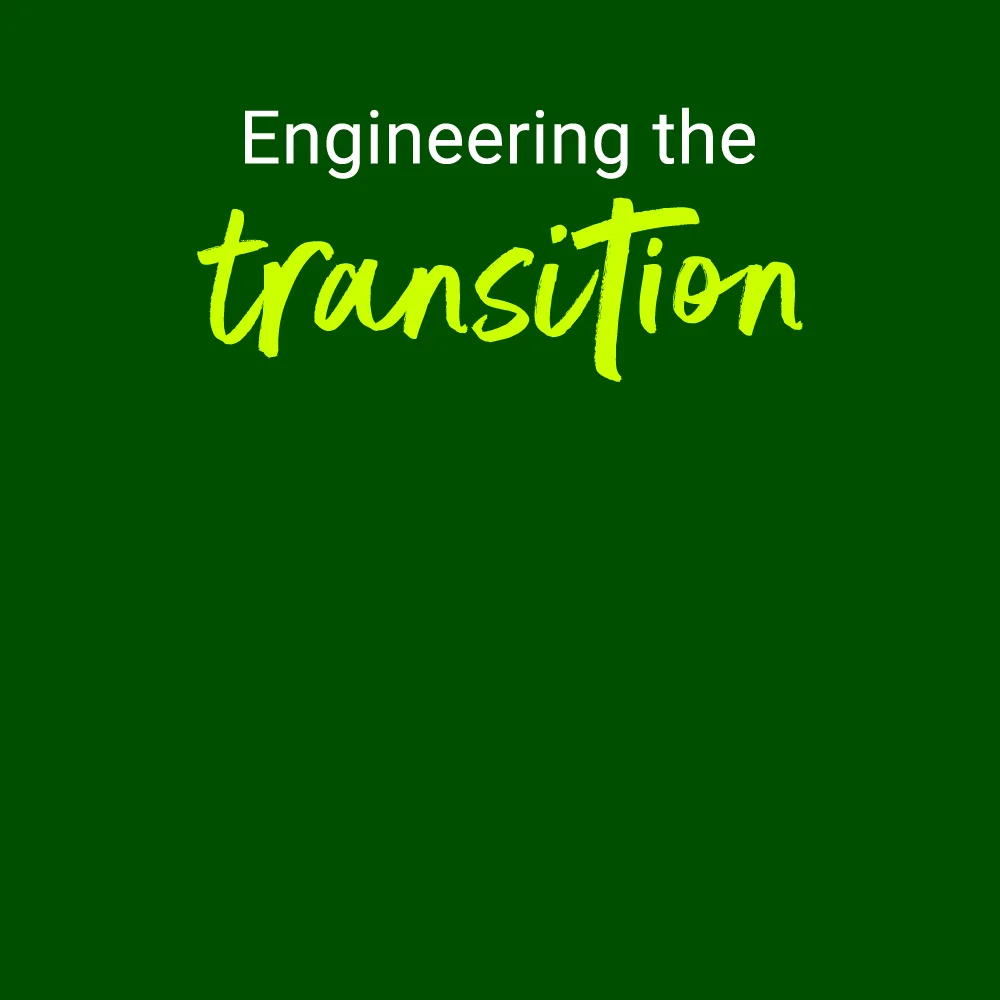

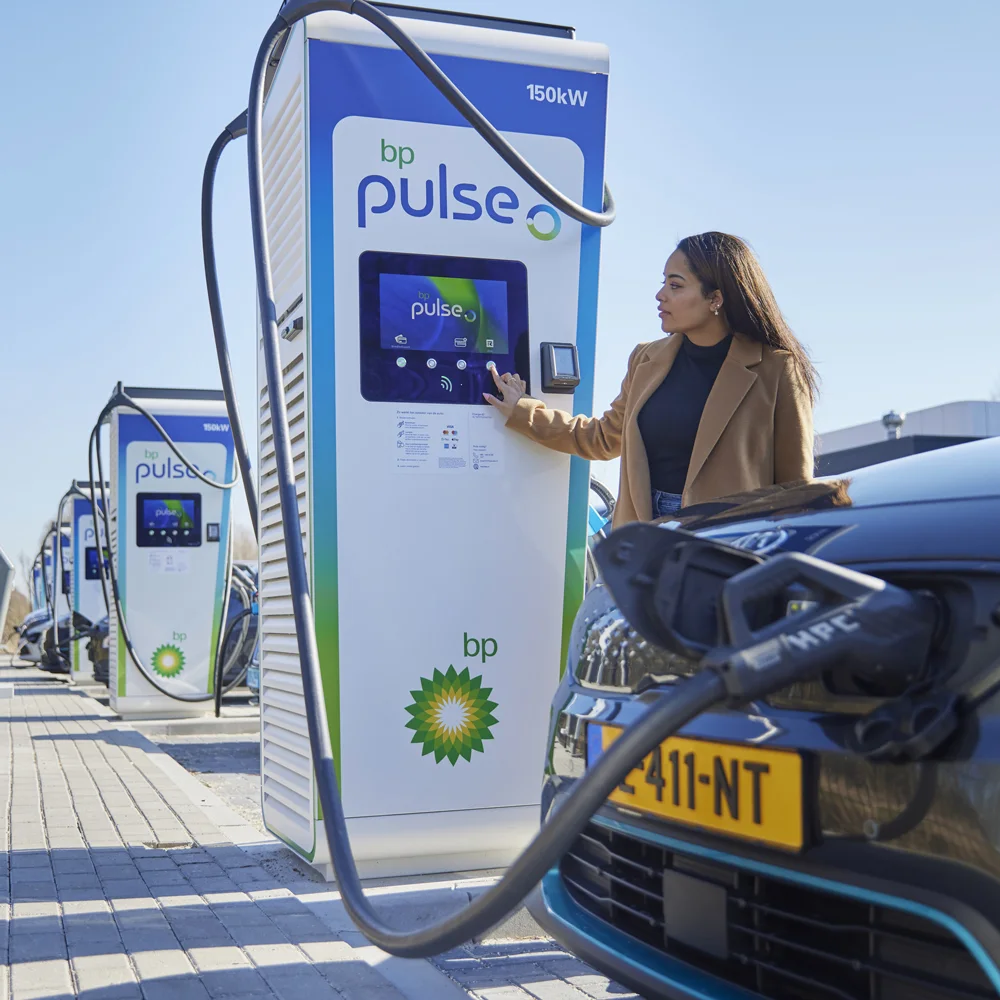
EV charging is still maturing, so we need to be constantly adapting and thinking ahead.”
Sikai Huang

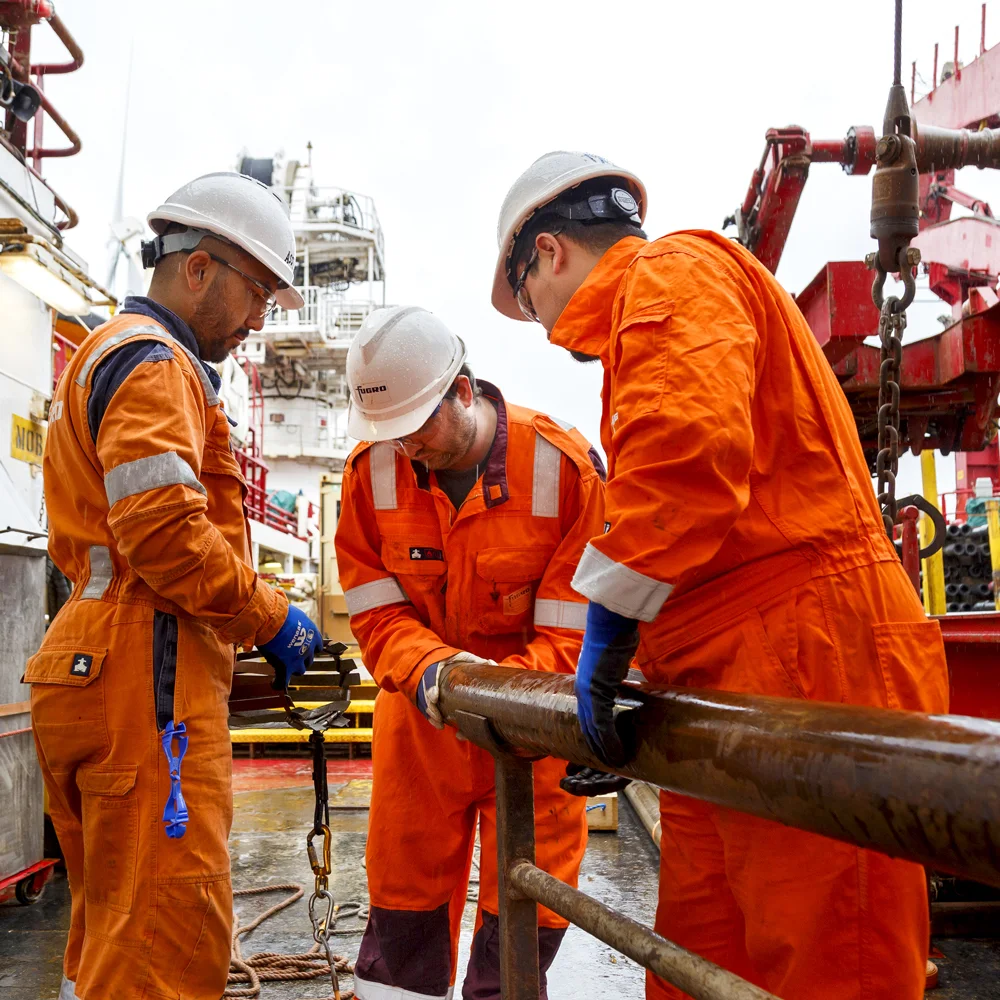
Managing power constraints in EV charging
SIKAI HUANG

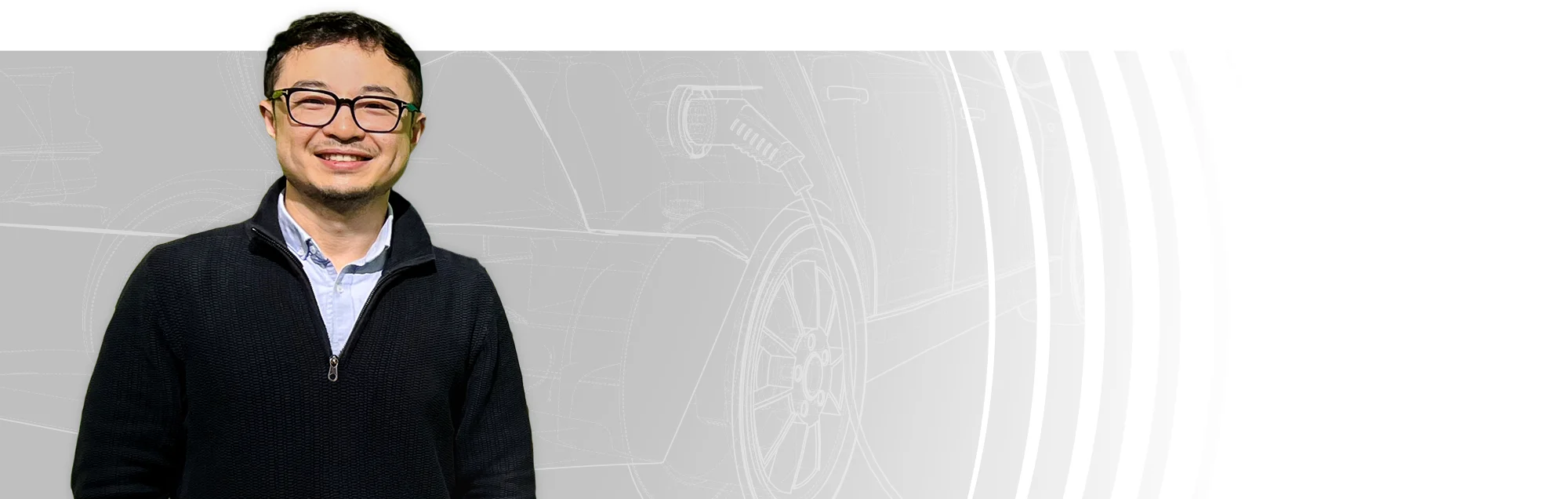
With the increasing number of electric vehicle drivers, including passenger cars and commercial vehicles, how can bp pulse cope with the power demand on charging infrastructure and allocate the most accurate amount of power available at each charging site?
It’s product manager Sikai Huang’s job to figure that out.
Power constraints are one of the biggest obstacles to rolling out EV charging infrastructure, and power grid operators aren’t always able to provide all the power needed. So, Sikai and his colleagues are building software for the future to ensure customers still have an extraordinary charging experience, even when demand is high.
“Our charging management software will enable customers to charge their vehicles at the maximum power available on site without tripping the fuse. Customers won’t notice – but we’ll stay safely within the power limits for each site,” says Sikai, who is based in London for bp pulse.
This is just one of the issues that Sikai and his colleagues are focusing on. They’re also looking at potential solutions for problems that could arise in the coming years, including changes to smart electric vehicle charging technology and power grid operation regulations.
“EV charging is still maturing, so we need to be constantly adapting and thinking ahead,” says Sikai. “Electric mobility is an important piece of the global energy transition puzzle; the question is how we do it.”
Back to top
Laying the groundwork for offshore wind projects
ANDREW DEEKS

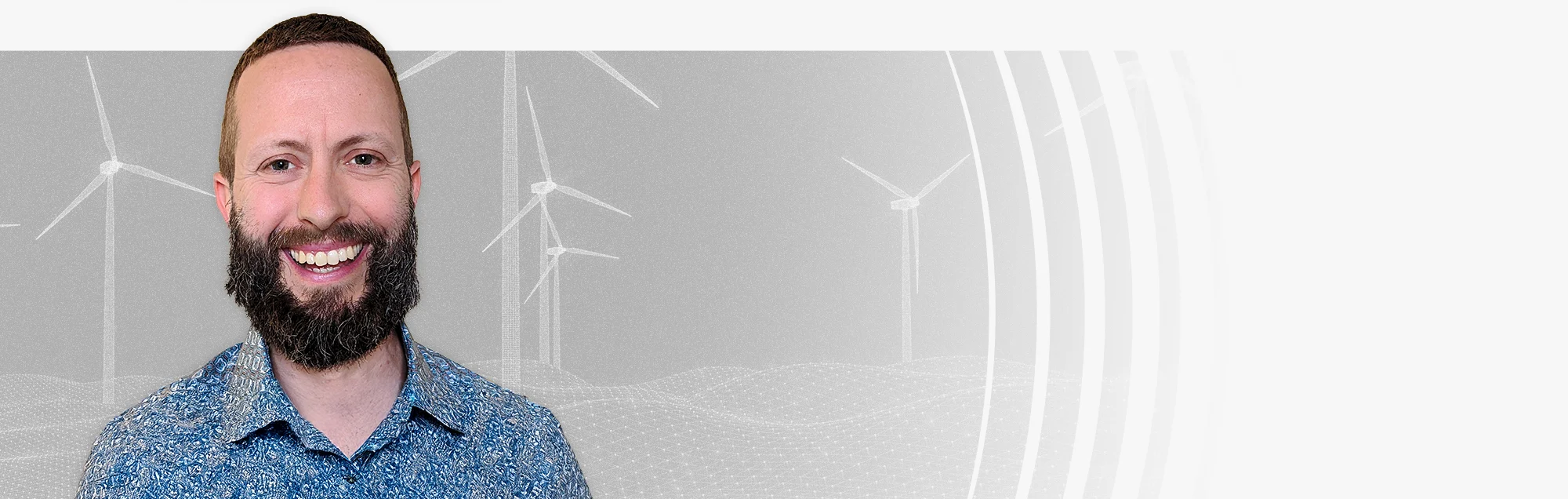
How do you install hundreds of structures in the middle of the sea that are as tall as a skyscraper?
That’s the challenge facing geotechnical engineer Andrew Deeks. His role is to study the strength and safety of the ground ahead of offshore wind turbine installations.
Once they have the necessary internal and external consents and approvals, bp and partner EnBW plan to install between 100 and 200 wind turbines in the Irish Sea for the Morgan and Mona offshore wind projects. To fully understand the make-up of the ground, samples need to be taken and tested.
Together with his colleagues, Andrew has worked with contractor Fugro to drill around 100 boreholes into the seabed with a new technique that is designed to help to more safely recover higher-quality soil and rock samples from the seabed. Instead of requiring a second rock-drilling rig, the new technique uses a single system that can sample and probe soil and rock, recovering high-quality samples in a single pass, with reduced exposure to personnel.
This project alone is about three times the size of bp’s usual sample drilling activities in a year, and this new technique can also potentially be used for any upcoming oil and gas projects. After the samples are taken, they are analyzed at a lab on the vessel and onshore, and that data is then studied by bp teams.
“What makes this project unique is its scale. We are looking at potentially putting turbines across a 308-square-kilometre site, so it’s a large area to work across,” says Andrew. “Using the survey data, we will work closely with our structure design and transport and installation teams to find the best overall solution for the planned site.”
Putting safety first in mobility and convenience
SILVIA BORDES CABRERA

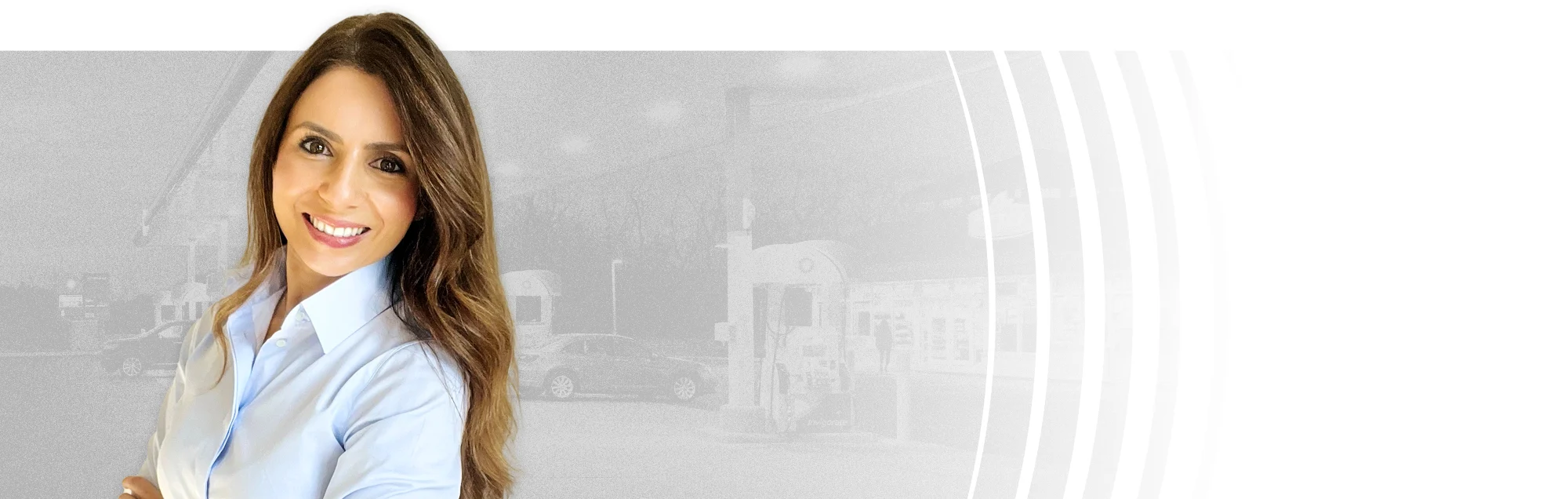
Millions of customers stop each month at bp retail sites around the world to fill their tanks and buy food.
As we grow the number of strategic convenience sites globally, one of Silvia Bordes Cabrera’s challenges is supporting the safe construction and maintenance of these new forecourts.
bp’s forecourts pack a lot of infrastructure into a small space. Fuel tanks, pipelines, pumps, canopies, shops and more all fall under Silvia’s remit. She is responsible for the global engineering guidelines and standards governing the forecourts and also looks at their general design.
“Safety is always my first priority,” says Silvia, who is based in Madrid. “That includes the safety of bp employees, customers, maintenance workers and anyone who is on site. My goal is to develop engineering guidelines that help to make our retail sites safer and more efficient – contributing to our ambition of becoming first choice for customers on the roadside.”
Silvia’s role includes both civil and mechanical engineering and a big part of her job is to facilitate co-ordination between the many different regions where bp is, so there is consistency between them.
“Without roles like mine, we could be working in a very isolated way,” says Silvia. “Small details can make a big difference and having a standardized approach to retail site engineering benefits everyone.”
Keeping tanks secure and intact
MANUEL FIGUEROA

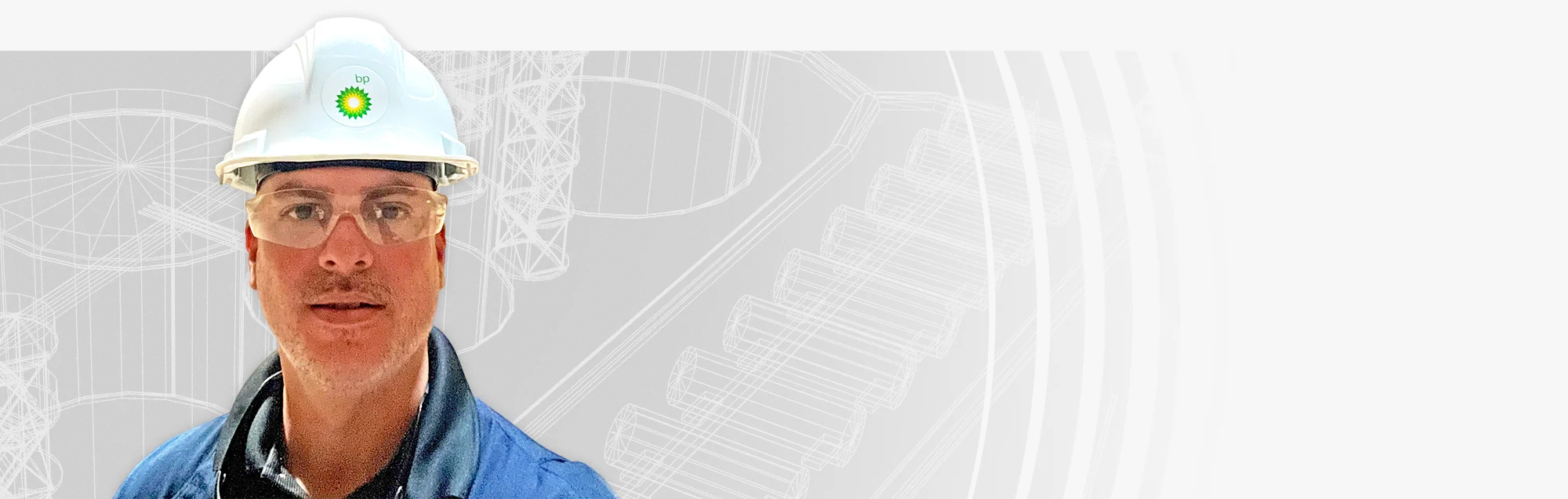
How do you prevent massive storage tanks from leaking potentially hazardous materials?
That’s the challenge facing asset integrity engineer Manuel Figueroa.
After gasoline and diesel are refined, they are often stored in tanks before being delivered to customers. Manuel helps to keep these storage tanks safe, well-maintained and protected against corrosion through regular inspections, maintenance and repairs.
“The tanks vary in size from about 40 feet (12 metres) in diameter to the size of a baseball field and store a range of fuels, from crude oil to gasoline to jet fuel,” says Manuel, who is based in Chicago. “There is a lot of knowledge that’s specific to storage tanks and understanding that and staying on top of it can feel like getting another engineering degree.”
Tanks get regular visual inspections and then a full, detailed inspection and maintenance work-up on a risk-prioritized basis. That can include comprehensive leak checks in and around the tank, and the application of new coatings.
The American Petroleum Institute sets out very detailed guidelines and recommendations to maintain the tanks and those standards are often used globally, too. That’s partially why Manuel works closely with colleagues from abroad, as far away as South Africa and France.
“One of the parts of this job I enjoy most is sharing knowledge with our teams overseas and breaking down the requirements so everybody can understand how and why we do what we do,” he says. “To have a positive influence on the way we work around the world is very fulfilling.”

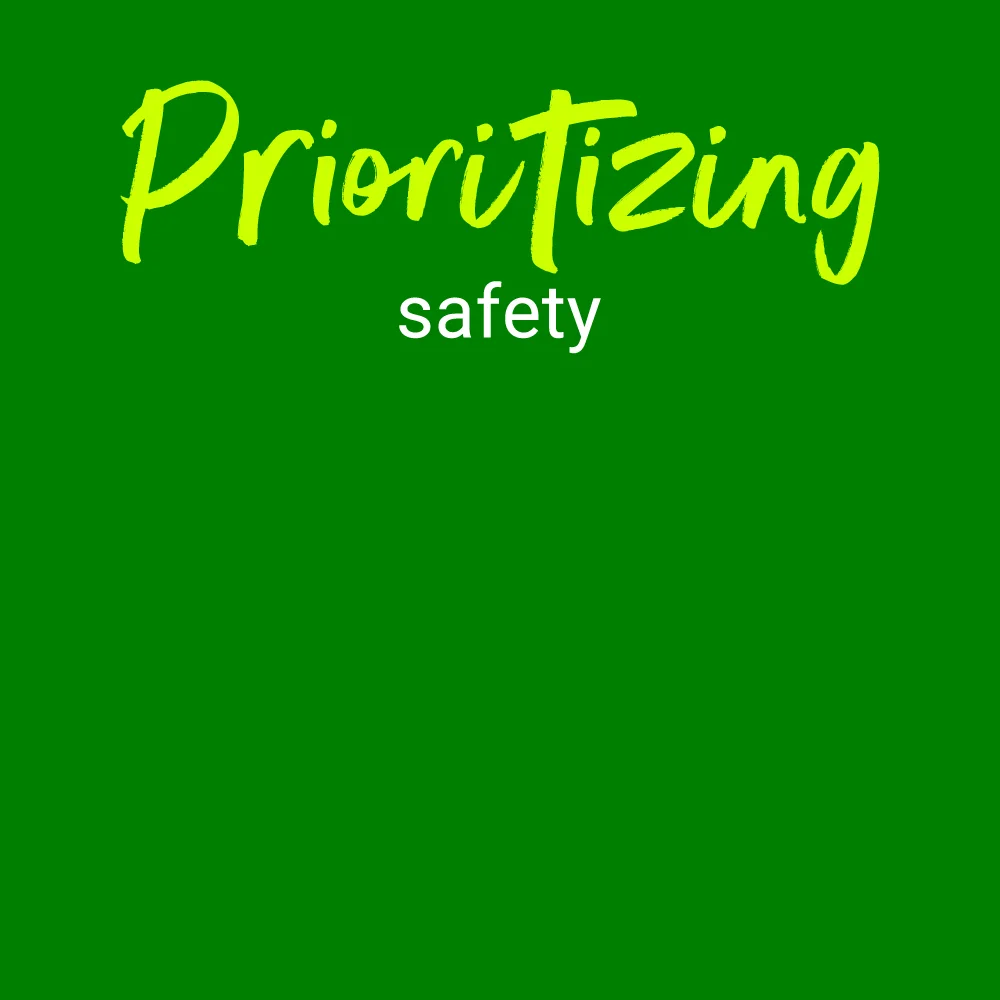

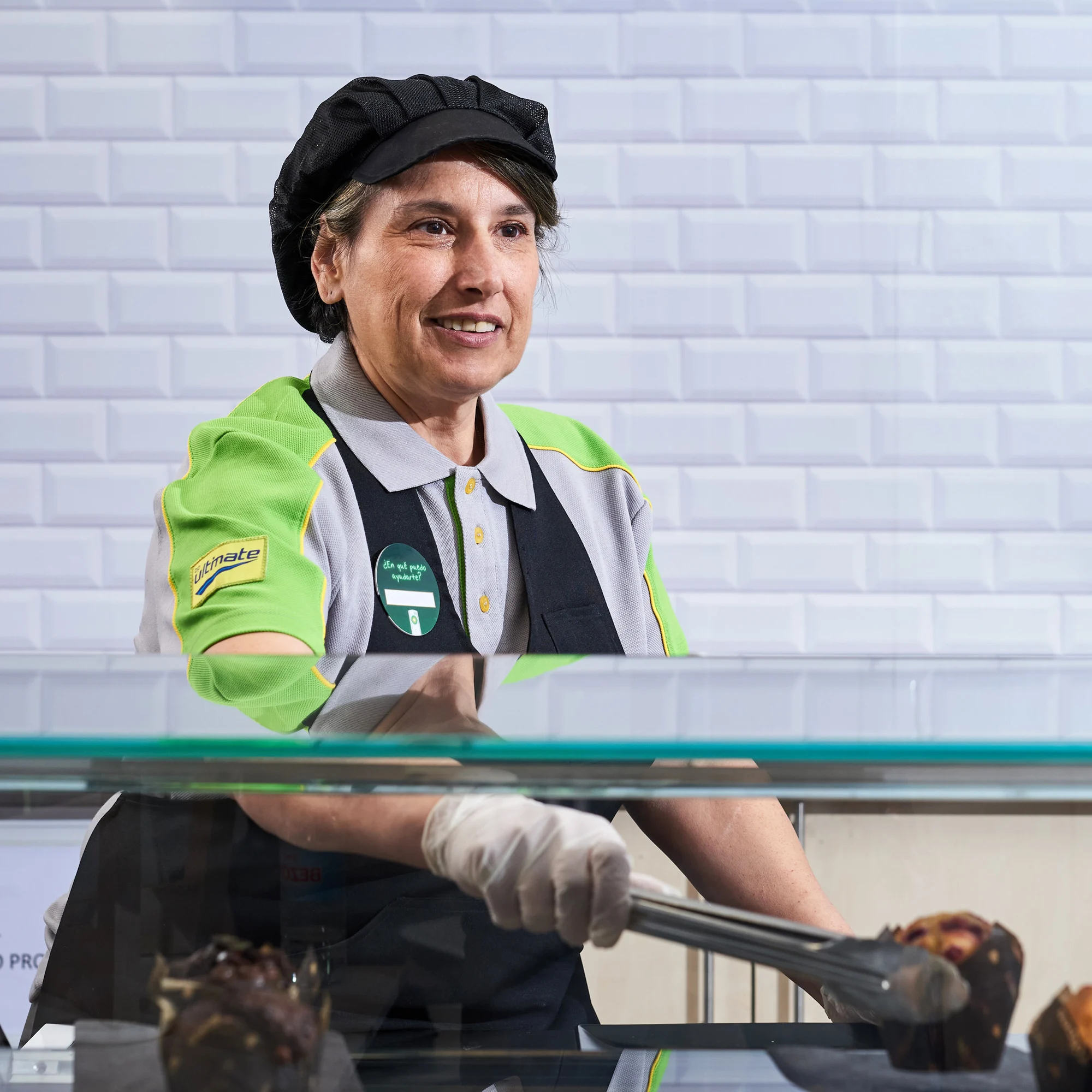
Safety is always my first priority. That includes the safety of bp employees, customers, maintenance workers and anyone who is on site.”
Silvia Bordes Cabrera

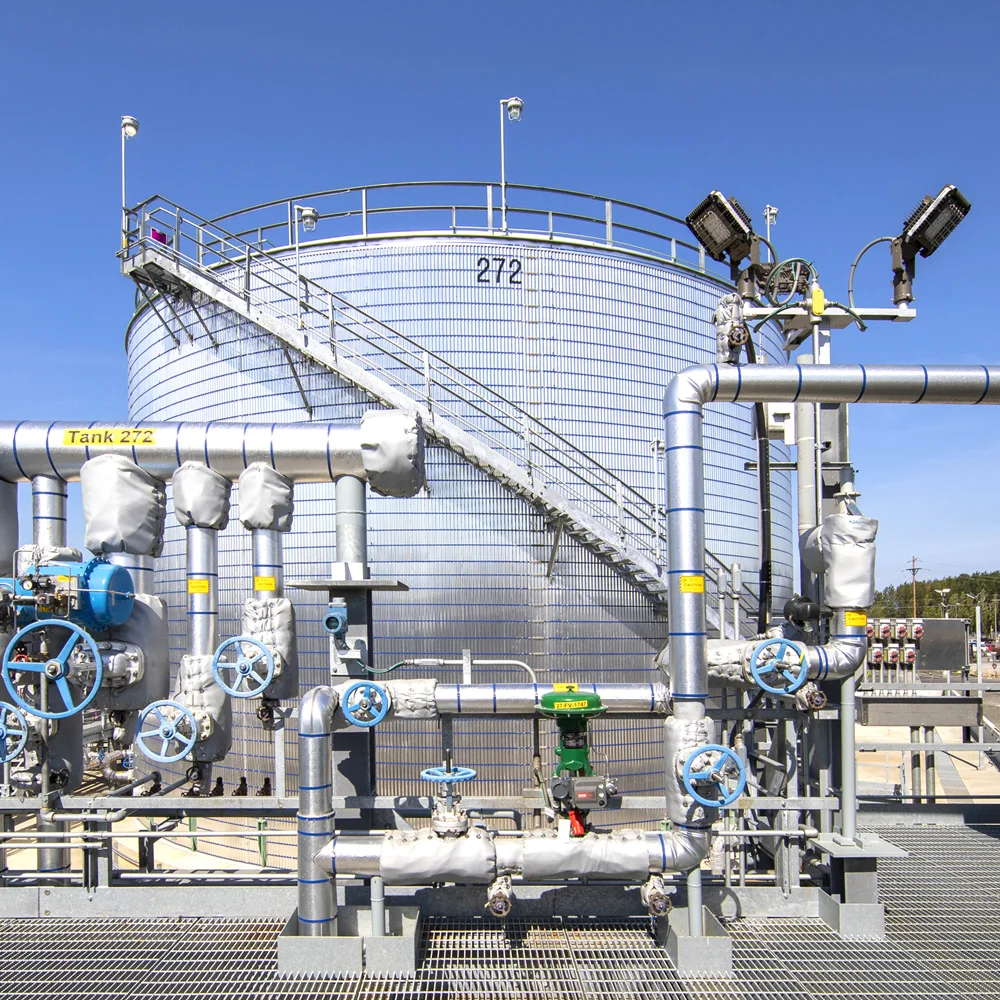
While today we’re mostly in oil and gas, we increased the proportion of our global annual investment that went into our lower carbon and other transition businesses from around 3% in 2019 to around 23% in 2023.